SRNL Granted Patent for Innovative Additive Manufacturing
Additive Manufacturing (AM), sometimes referred to as 3D printing, is a novel method of manufacturing that has grown considerably in recent years. A team of five scientists from Savannah River National Laboratory (SRNL) was recently granted a patent on behalf of Battelle Savannah River Alliance (BSRA) for a new, innovative approach to AM. The team includes Donald Benza, Aaron Washington, Jonathon Baker, Camden Chatham and Adrian Mistreanu.
AM differs significantly from traditional bulk manufacturing methods. Whereas traditional formation of components begins and ends with a single piece of material, AM fabricates material in a layer-by-layer process.
“What we were looking at is how can we move AM into the future,” said Benza, senior engineer in SRNL’s Imaging, Radiation Systems and Robotics group. “Instead of being a replicating tool, can we look at it as a way that we can take advantage of all these interesting new effects that are being built into parts . . . and actually create new materials and parts that were not possible through traditional manufacturing.”
Methods such as injection molding or computer numerical control do not readily lend themselves to alteration of building materials as they are formed in place. This includes not only the piece being manufactured itself, but also its physical properties, such as strength and flexibility. While typical AM methods afford some ability to alter these properties in the manufacturing process, there are still limits on the possible extent of alteration. As the layers of material are each deposited, the parameters of the adherence of each layer on top of the previous layer stay the same. Thus, the physical properties essentially stay the same throughout the deposition process and, as such, any further modifications to the product must be done after the build is complete.
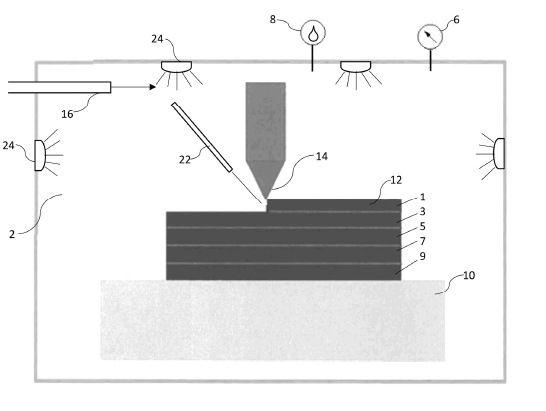
Schematic showing the novel AM process (image Donald Benza)
The SRNL team’s new AM approach introduces a chemical or atmospheric treatment between layers. This affects a thin section of the deposited layer, down to 300 nanometers of depth, which causes a modification in the chemical structure of the polymer build material. The depth of the chemical modification can be manipulated through a change in the formation parameters. Inside the AM chamber, pressure can be increased, humidity can be decreased, and temperature can be altered. Energy can be delivered to have the sought after effect, such as microwave, infrared, visible or x-ray. This creates a superior product over both traditional bulk manufacturing methods and the AM methods currently in use.
The new AM approach allows flexibility in how the treatment is applied. It can be present across the entire depth of the build or across a gradient within the product. The applications for this approach are vast and may represent a next generation of AM. All manner of industries can benefit.
“Improvements from this technology provide versatility in the manufacturing process,” said Benza. “The resulting products can be more valuable as a result.”
In addition, classes and types of materials previously thought unsuitable for AM may now be considered for use. Polymers that were not thought to possess the desired performance characteristics for traditional AM may now be in play. This could lead to much higher performance, including better mechanical properties, temperature resistance, chemical resistance and radiation resistance, as well as a combination of these characteristics.
The possibilities and applications of these new AM techniques are seemingly endless. Not only can an infinite combination of treatments be applied, but all manner of starting feedstock can be used. Plastic waste that would end up in a landfill can be shredded and melted down into a useful part. Benza indicates that this technique could even be used in deep space missions.
“There are so many applications out there,” said Benza. “It just depends on your imagination and knowledge of chemistry.”