“Advanced manufacturing is about discovering new processes, pathways and approaches for carbon-neutral manufacturing outcomes.” – Sue Clark, SRNL Deputy Director of Science and Technology
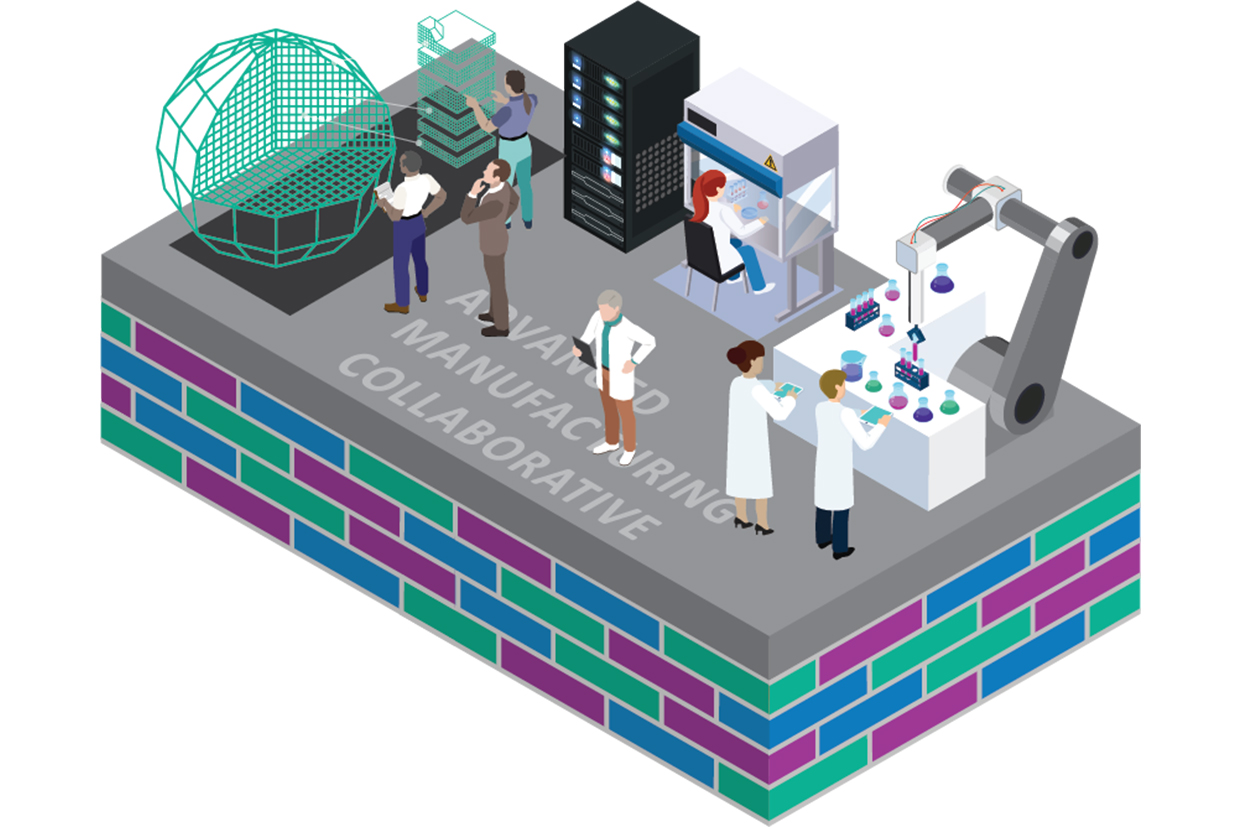
graphic: Susanna King, SRNL
Future manufacturing technologies for the Department of Energy’s Office of Environmental Management took a giant step forward recently as site work began for the construction of the Savannah River National Laboratory’s Advanced Manufacturing Collaborative on the University of South Carolina Aiken campus.
“Advanced manufacturing means many things to many people, and there are a number of notionally similar capabilities across the country and with other national laboratories,” said Vahid Majidi, Director of Savannah River National Laboratory. “But what really sets our AMC apart is its focus on reducing the carbon footprint and moving toward a manufacturing environment where energy associated with production and the feed materials, all have a very low or zero carbon footprint,” said Majidi. ”Reductions in a carbon footprint in itself is a significant goal to meet many of the DOE’s future needs in environmental cleanup.”
There are many ways to reach a zero carbon goals, and the AMC will help generate unique pathways to that end. Majidi said the AMC will help industry achieve this end through several mechanisms such as:
- Low-Carbon Waste Forms
- Bio Manufacturing
- Alternative energy sources, including Fusion
- Energy Storage
- Process Intensification
“Advanced manufacturing is about discovering new processes, pathways and approaches that can lead to manufacturing outcomes that enable carbon neutrality,” said Sue Clark, Ph.D., Deputy Director of Science and Technology at Savannah River National Laboratory.
When describing advanced manufacturing, Sharon Marra, Deputy Laboratory Director for Operations at Savannah River National Laboratory, pointed to process intensification.
“It’s about taking traditional manufacturing methods and modernizing them in terms of making them smaller, modular, more efficient, more cost effective, and perhaps more integrated,” she said.
“SRNL is uniquely good at process intensification,” said Majidi. “This is where we reduce the carbon footprint by increasing the efficiency of manufacturing’s chemical and physical processes.” Increasing efficiency in these processes has the potential to reduce or prevent waste, thereby reducing or eliminating the need for environmental cleanup or remediation.
But increasing efficiency of processes isn’t the only way SRNL will help get to a zero-carbon footprint. SRNL is also ensuring the AMC building itself has the lowest carbon footprint possible.
“The building itself will be LEED [Leadership in Energy and Environmental Design] certified so that the building will use less energy and be more efficient,” he said. “We will monitor all the processes happening in the building, and we’ll also monitor the building itself through various sensors feeding into a well-curated cloud database. This allows us to use artificial intelligence to optimize manufacturing conditions and identify energy efficiencies in near real time,” said Majidi.
Materials substitution is another mechanism through which a manufacturer can achieve a lower carbon footprint.
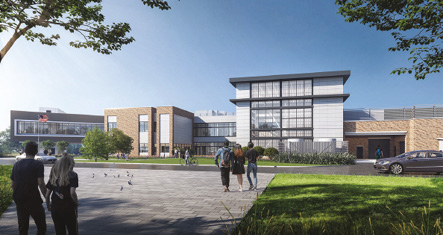
“We are researching biomanufacturing techniques to produce a library of fine chemicals used in standard manufacturing processes. We will discover ways to apply non-fossil fuel-based hydrocarbons that will feed modern processes familiar to industry to produce the materials we all use every day,” said Majidi.
With increasing use and reliance on automation, cyber security is a concern for integrated control systems employed on most modern manufacturing floors. A key element of SRNL’s AMC will be a strong layer of dynamic cyber security that will protect all of the automated chemical and physical processes.
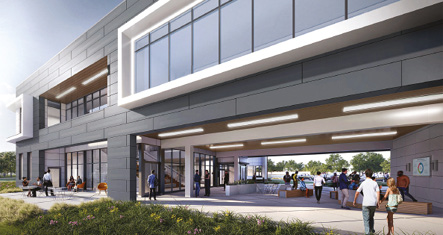
Architect’s renderings of what the completed AMC will look like
“With that threat in mind we will develop a robust cyber defense approach to protect our systems and recognize intrusion attempts; the goal is to prevent unauthorized access to our manufacturing processes,” said Majidi. ”By building and demonstrating cyber security around programmable logic controllers, digital relays and industrial control systems, we will support industry’s need to ensure uninterrupted operation while maximizing the quality of manufactured items.”
Located on the University of South Carolina Aiken (USCA) campus, the 60,000-square foot building will be the result of a close partnership between the Department of Energy Office of Environmental Management (DOEEM), USCA and North Wind Construction Services, LLC. The location was selected to maximize the AMC’s impact for industry, academic community, and SRNL.
“Perhaps the biggest advantage of the AMC is that it will be on the University of South Carolina Aiken’s campus, which opens a brand-new opportunity to directly interface and collaborate with students,” said Majidi. “We are looking at this as an educational gateway and future pipeline for SRNL and the Savannah River Site, that will bring new ideas to the Department of Energy.”
Marra said having access to the university’s students and developing the next generation of researchers, engineers and scientists was at the forefront of the decision to have the AMC at the university, giving SRNL access to potential interns, graduate students, postdoctoral candidates and the students in general, while giving them access to potential mentors, hands-on, real-world experience, and career opportunities.
“The AMC will be a place to bring together a diverse group of people to solve problems including industry, academia and SRNL to learn how to make processes work better, or create new ones, in order to manufacture in a more cost effective and efficient manner,” said Marra.
“This is the kind of environment where a national lab can come together with both industrial and academic partners to accelerate discovery and demonstrate solutions for industry more rapidly than if we were trying to do so on our own,” said Clark.
“The AMC allows our researchers to collaborate with industry and academia in a more accessible and open space than behind the fence at the Savannah River Site. said Marra.
To the casual observer, the nexus between the DOE-EM mission and advanced manufacturing may not be readily apparent, but to Majidi it’s crystal clear.
“DOE-EM’s mission is to deal with legacy [nuclear] waste generated during the Cold War,” said Majidi. “What we’re focusing on are future processes that minimize, reduce or eliminate waste altogether. So, if we can develop separation processes that minimize the waste, if we can develop manufacturing processes that minimize the waste and its associated carbon footprint, then we have integrated total waste reduction of into those processes. EM is the driver for reducing or eliminating future waste resulting from activities we are doing today. EM is working today to deal with the legacy of waste left behind. Our goal [AMC goal] is to not leave legacy waste behind for the future generations,” he said.
Reductions in manufacturing’s carbon footprint and reducing the need for remediation of waste from manufacturing are significant milestones for our nation, and the AMC advances our economic competitiveness as well.
“Two of the major expenses in manufacturing processes are energy input and waste disposition. Regardless of if you’re an environmentalist or not the processes that involve energy reduction and waste reduction ends up always saving production costs at the end of the day. Processes developed at the AMC are going to reduce costs,” said Majidi.
Because of its location on the university campus and collaborations with industry and academia, the activities in the facility will involve non-radioactive systems, and information that can be publicly shared. These activities provide a foundation for discovery and advancement that can be used to accelerate innovation for manufacturing of classified and/or nuclear components and radioactive materials.
The Advanced Manufacturing Collaborative is slated for completion and occupancy in fiscal year 2025.