The Nuclear Paradigm Shift: SRNL Modular Systems Transform Global Security
“The modules are a small footprint, so we can test things that other larger facilities can’t test, such as radiation monitoring equipment or glove box processes.” – Doug Lowry
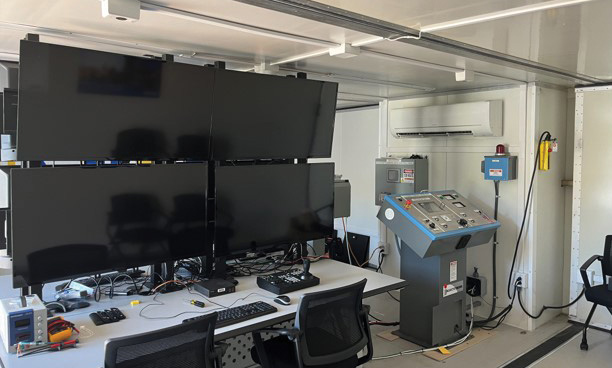
A look inside the control module of the Mobile Melt Consolidate (MMC). (SRNL)
In 2006, the Department of Energy sought a way to obtain excess plutonium from around the world in the safest and quickest way possible. The Savannah River Site, with more than 70 years of experience with plutonium, was the answer. Through the National Nuclear Security Administration’s Office of Material Management and Minimization (NA-232), or M3 for short, DOE set out to work with partners to “minimize the need for, presence of, or production of weapons-usable nuclear material around the world.” For the past 15 years, Savannah River National Laboratory, through the Global Security Directorate, has been a mainstay of this mission through deployable modular systems designs and teams.
When the DOE request reached SRNL, the lab immediately began developing a concept that would eventually become the first nine modules of the Mobile Plutonium Facility. The facility is the only one in the world that can support the safe characterization, stabilization, and packaging of weapons-grade plutonium material through rapid response deployment.
“When a country is identified by M3, the MPF will be ready to be deployed within 30 days’ notice,” said NA-23 Portfolio Manager Doug Lowry.
The MPF’s modules contain specialized equipment, from gloveboxes, to x-ray equipment, to a standalone power grid, to successfully recover and remove the plutonium (Pu) and safely package and store it until disposition decisions can be made.
Today, the MPF team, which consists of about 30 members, has enhanced operations of the system by adding an advance Remote Recovery team that can recover small amounts of Pu materials quickly while waiting for the rest of the MPF team to arrive on site. With the acquisition of Boston Dynamics’ Spot®, a four-legged robot that resembles a dog, the team now has a small, easy to deploy kit that will provide operational awareness for the MPF team. It also reduces human exposure to radiation and other hazards while the material is removed and moved to a safe location for further processing. Its autonomous operation allows the team to focus on data analyzation while Spot handles the physical inspection of the facility location.
The deployment of the MPF on several exercises sparked the idea and conception of the team’s next material minimization project – the Mobile Melt Consolidate system.
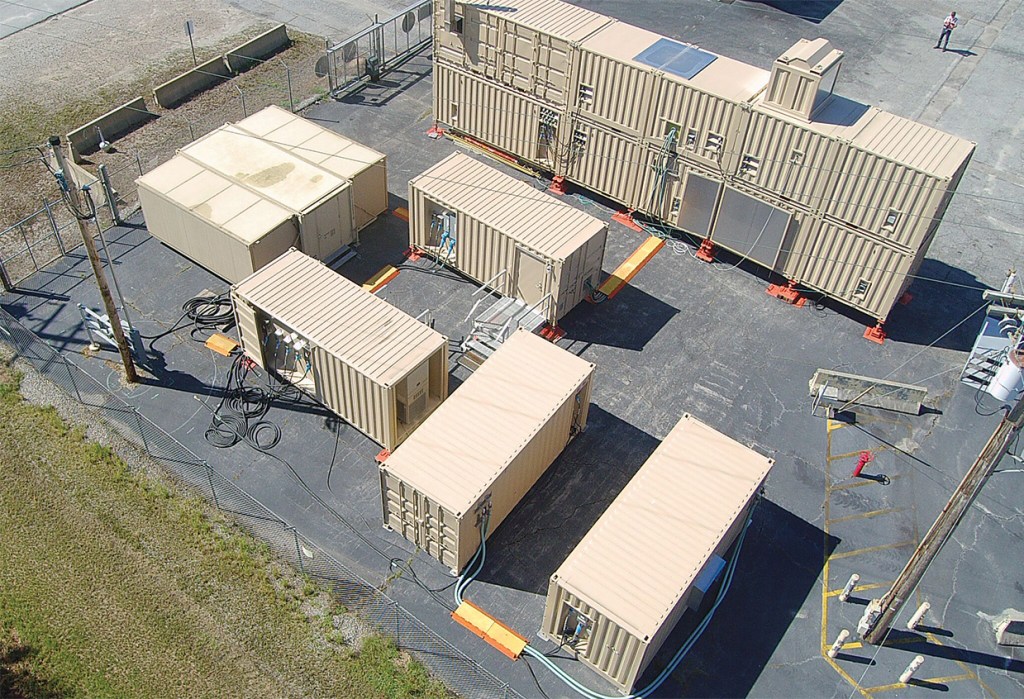
An aerial view of the Mobile Melt Consolidate. The system is made up of a collection of modules that work together to melt down spent nuclear fuel. (SRNL)
Like the MPF, the MMC is a one-of-a-kind, true modular system that can be transported to different parts of the world, but this technology aims to transform highly enriched uranium to more stable LEU forms, supporting nonproliferation goals. The MMC is a collection of modules – furnace, control, pump, cooling, etc. – that melt down the spent nuclear fuel. This allows countries to store the materials in a more stable and safer configuration. It is built to fit within the bounds of a specified country’s placement area and run on that country’s power grid.
The current iteration of the MMC requires about 15 people for operation throughout the modules. Once each new country is identified, the team will get started on the next build based on the outlined dimensions and enhancements needed for the specific location.
Finding the Design Sweet Spot
Both the MPF and the MMC module designs have challenged the GSD team to conduct extensive research and experiments with an array of solutions to ensure the systems performed at the highest capacities.
Unlike the MMC, which is built around the provisions of one country at a time, the MPF is designed for usage anywhere it is deemed necessary. The design of the MPF modules has gone through a series of modifications and testing to ensure its sustainability. The MPF team has tested the facility in the frigid temperatures of Alaska, the dry heat of the Nevada deserts, the dampening humidity of Key West, and the rocky waters of the Atlantic Ocean.
“Our first modules were built by Site construction, but we found out there are so many fabricators who could construct so many other types of modules,” Lowry said. “For example, we learned that we could get three modules built that could replace nine modules that we had previously built.”
Lowry and his team have worked with specialized manufacturers of International Standards Organization containers and modular buildings across the U.S., as well as companies that produce specialty equipment like glove boxes, nitrogen generators and automatic transfer systems. Bringing the companies together in a partnership has increased innovation and productivity.
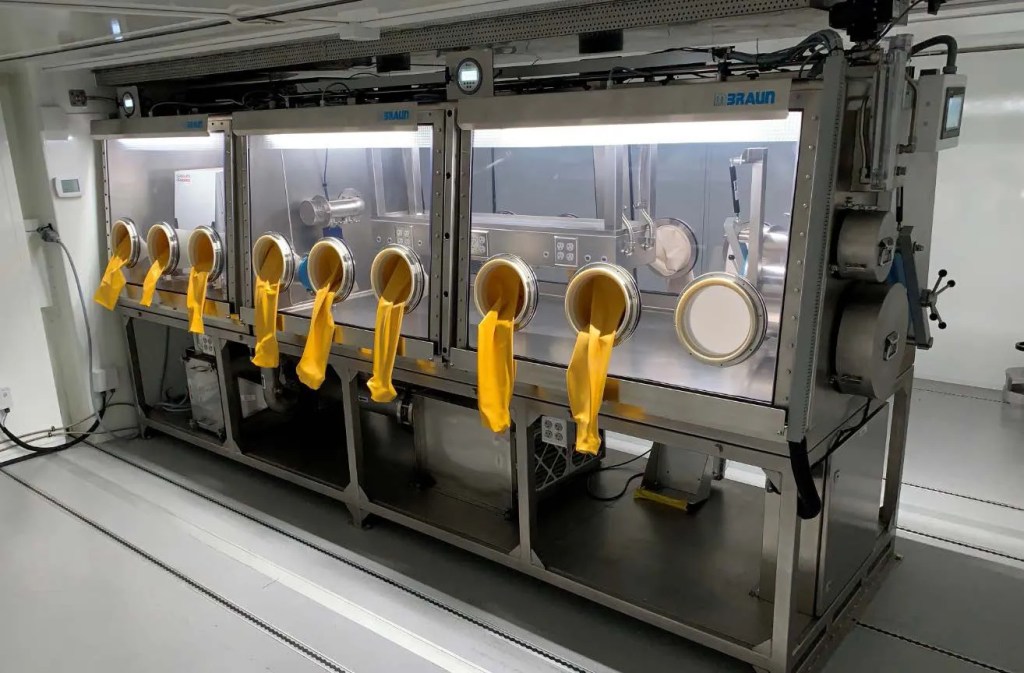
Glove boxes inside the Mobile Plutonium Facility (MPF) are used to do testing of nuclear materials on a small scale. (SRNL)
“We’ve gotten a glove box built and shipped it to the module manufacturer, where a module was already built. They would then cut the roof off the module, use a crane to lower in the glove box, and then build the roof back on,” Lowry said. “Now, we have a really good module to complete glove box missions within a much smaller footprint in terms of shipping, but a bigger footprint to operate in because they’ve designed special fold out modules.”
Because the team has moved to a design build concept, it has lowered costs, which allows for elevated efficiency. All specifications of module designs are now bid out to different contractors and all factory acceptance testing is done on the vendor’s site. Once complete, the modules are shipped to SRNL where team members are then trained on the module.
“[The MPF] gives us the ability and platform to go all around the world with a much lower budget than building a nuclear facility that would stay in one place. We’re able to design it, get it built, and once we do it for one country, we can make some tweaks and build another for a different country. With this concept, the cost is greatly reduced, which means we can do more work, and the timeline to do it is significantly lower,” Lowry added.
Convert, Remove, Dispose
The NA-23 program is executing its mission through a three-prong approach: convert, remove, and dispose. With SRNL’s extensive history in nuclear materials management, there are knowledgeable teams currently working within or working toward contributing to all three mission areas.
The use of advanced small modular reactors is an integral part of providing affordable and safe nuclear power options across the world. Lowry says these reactors are a part of what they have been working on recently, trying to utilize the lessons learned in the MPF and MMC program in modular system design and shipping strategies. GSD experts are also aiming toward converting large reactors, which use HEU and turn it into LEU, into small reactors that can be deployed as needed.
“We’re figuring out how to partner with organizations and take the things we’ve learned about setting up and shipping nuclear facilities,” Lowry said. “We can share those technologies with the vendors who are designing the modular reactors.”
The MPF and MMC are currently operating to fulfill the removal goal. They have been meticulously designed to be set up in a country to remove special nuclear materials and create a safer environment.
When it comes to the disposition of materials, the GSD team has been working with a group in the K Area Complex at SRS. The Site’s goal is to get rid of almost 57 metric tons of plutonium materials, so they called on SRNL to help in the design of a system that can increase throughput, reduce dose rate exposure to employees, and monitor hold up in the process lines to make these processes safe for operators.
“The modules are a small footprint, so we can test things that other larger facilities can’t test, such as radiation monitoring equipment or glove box processes.” Lowry said. “We’ve been able to pilot things on a much smaller scale so the bigger facilities, like those in K Area, can benefit from them.”
Uniquely Positioned
The move forward to securing new projects is intimately related to SRNL’s long-term history with modular systems. The knowledge that has been generated over time and through trial and error has positioned SRNL as modular experts for other government agencies to model their potential systems after.
“We have built a core set of engineers, E&I [electrical and instrumentation maintenance] people, maintenance mechanics, operational, and RADCON [radiological control] people who have all these lessons learned from the last 15 years. So, when it’s time for a new design, [our team] can say ‘we learned this in the desert or in the arctic, and these are things you need to think about.’ That way we can help the vendors understand our needs better, and then they have good methods to build the modules,” Lowry explained.
The SRNL Packaging Technology Group is also an invaluable asset to the modular systems team. Lowry says the luxury of having specialists within the lab who understand the nuances of nuclear materials and how to safely package and transport them is what separates SRNL from commercial modular system providers.
“Our vision is to grow the modular team so we can keep a core group that retains knowledge and is continuously learning. That way, when other agencies want to take on projects, we can be on their team and share our knowledge. It’ll almost be like a mentorship, and that’s where we want to get,” Lowry said.