“The intent was always to treat the waste and dispose of the waste in an environmentally stable form,” – Daniel McCabe, SRNL Scientist
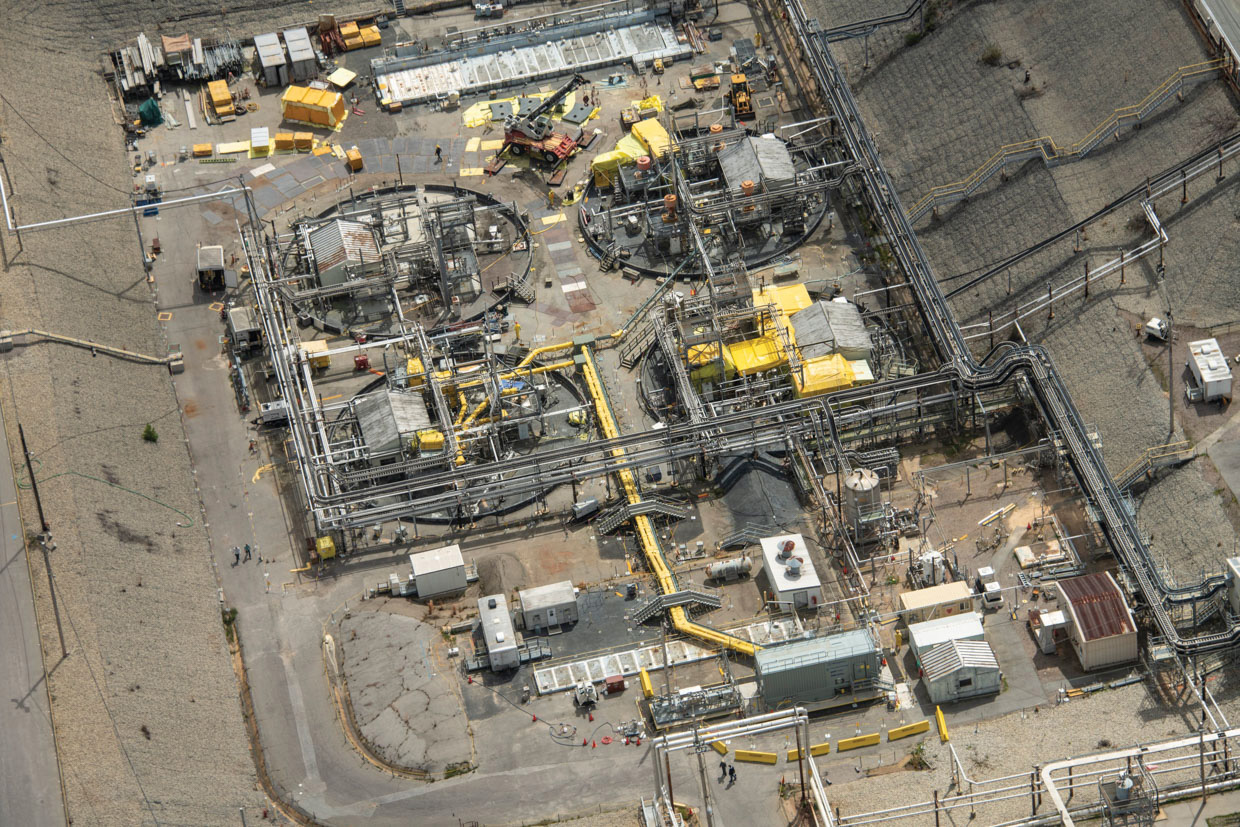
H-Area Tank Closure Cesium Removal. photo: Savannah River Site Photography
For as long as scientists have worked to develop nuclear energy and nuclear weapons, scientists have also labored to develop effective means of disposing of nuclear waste products. This need is the mission of the Department of Energy, Environmental Management (DOEEM), “to complete the safe cleanup of the environmental legacy brought about from decades of nuclear weapons development and government-sponsored nuclear energy research.”
One solution to the problem, a problem that was decades in the making, also required decades of work to resolve. Recent news articles heralded the start of the “first large-scale pretreatment” of millions of gallons of radioactive waste stored at the Hanford and Savannah River (SRS) sites. Largely missing from that mainstream media coverage is discussion about the years of technology development and refinement that make such milestones possible.
Cesium is present in the by-products of nuclear material production that have been pumped to waste tanks since the 1940s and 1950s. Modern-day processing of nuclear materials continues to produce liquid wastes requiring storage and treatment. While storage tanks were built to safely hold these waste materials for 50 years, the reality is many tanks have reached or are reaching their planned lifetime, lending a sense of urgency to safely remove and treat the waste within them.
According to Daniel McCabe, Ph.D., senior fellow scientist at Savannah River National Laboratory (SRNL), Sandia National Laboratory and Texas A&M University first developed a synthetic inorganic ion exchange technology to absorb cesium – the primary soluble radionuclide found in the waste – that was subsequently deployed in practice for DOE. “The intent was always to treat the waste and dispose of the waste in an environmentally stable form,” said McCabe. “CST [Crystalline Silicotitanate ion exchange] is just one of the technologies developed to do that.
SRNL didn’t invent the technology, but SRNL did play a key role in maturing the technology, demonstrating its use, and providing engineering parameters that support design and safe operation of the technology. McCabe says SRNL has more than 80 published reports on CST and his first report on the technology was in 1995.
What is unique about CST, according to Frank Pennebaker Director, Chemical Processing and Characterization at SRNL, is that CST can be deployed near a tank and used there to remove cesium from the waste, thereby negating the need for removal and transport of the waste to another location for treatment. Deploying the semi-modular technology “at tank” provides savings in time and money, while reducing risk. Using CST gets the waste from a liquid to a more stable (and safer) solid state and ultimately allows for the closure of the tanks.
“At the Savannah River Site, the bulk of the waste is removed from the tanks,” said Bill King, a scientist in SRNL’s Chemical Flowsheet Development Group, “And the tanks are cleaned sufficiently for the state to approve the closure of the tanks.” According to Pennebaker, maximum removal is the state we want to get to – where most of the risk has been remediated.
While the CST technology was matured with the Savannah River Site in mind, the proven and scalable technology is also being used at the Hanford site and at Fukushima, Japan, as part of the cleanup from the 2011 tsunami-induced disaster.
There are 51 tanks at SRS, eight of which have been closed, with the goal of having them all closed by 2033. At Hanford, where CST was most recently deployed, there are 177 tanks needing to be closed.
McCabe said the first testing of CST for use at SRS was done in collaboration with the Oak Ridge National Laboratory April 25, 1997. “A lot of people have been involved for a lot of years. SRNL led the work, but there were contributions from Oak Ridge, Sandia, and PNNL, we’ve all done testing with it,” he said.
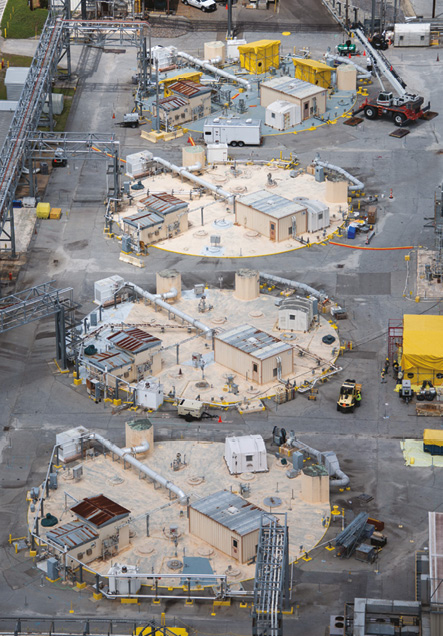
F Area tank farm at SRS. photo: Savannah River Site Photography
McCabe points to the early absorption testing in the late 1990s and the computer modeling SRNL did for the Hanford and SRS at the turn of the century as significant milestones in the 23-year project, as well as determining the proper CST column size to mitigate heat and dose effects. McCabe said there were multiple designs as the technology evolved, but the startup of TCCR at SRS marks the first time CST was built and operated in the DOE complex. The 2001 engineeringscaled demonstration, with a column of actual waste, marked another milestone in the project.
“The computer modeling allowed us to take small-scale experiments and scale them up to how an engineering scale process would perform,” said McCabe. Computer modeling was also used to validate recent assumptions to operate CST as efficiently as possible and optimize its use, which saves taxpayer dollars, according to Pennebaker.
The CST media is an inorganic, highly stable material that is highly selective for removing Cesium in tank waste solutions. The media absorbs Cesium, and development of an engineered form and large-scale production by UOP of Des Plaines, IL, U.S.A., was key to making the operations feasible.
“Cesium is typically the highest dose radionuclide in high-level tank waste – removing that Cesium from the tank waste is a big, big step toward the remediation of waste on site,” said King.
It has taken 25 years to perfect and implement the CST technology, and it is easy to lose sight of how, in the nuclear waste industry, it is not uncommon for solutions to take a long time to come to fruition. “In a career in this business, you might get to see one or two or maybe a handful of things actually implemented,” said King. “Because there are so many potential problems and potential issues in implementing any kind of technology in this environment, this is just the time scale you’re looking at. It’s just the reality,” said King.